Quality Tools That Transform: Mastering the 7 Essentials for Continuous Improvement
Simplify Problem-Solving, Drive Excellence, and Unlock Efficiency in Just 90 Minutes!
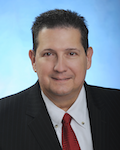
Instructor :
Jose Mora
Webinar ID:
12435
Date: APR 03, 2025 (THU)
Start Time: 10 AM PT - 11:30 AM PT
Duration: 90 Mins.
What will you learn
-
- Overview Of Continuous Improvement And Its Importance For Businesses
- Introduction To The Seven Basic Quality Tools And Benefits
- Detailed Explanation Of Each Tool’s Standalone Value And Use
- Understand How To Integrate Tools For Effective Problem-Solving
- Learn Through A Practical Example For Real-World Application
- Step-By-Step Guide To Using Tools For ….
-
- Overview Of Continuous Improvement And Its Importance For Businesses
- Introduction To The Seven Basic Quality Tools And Benefits
- Detailed Explanation Of Each Tool’s Standalone Value And Use
- Understand How To Integrate Tools For Effective Problem-Solving
- Learn Through A Practical Example For Real-World Application
- Step-By-Step Guide To Using Tools For Process Improvement
- Interactive Q&A Session To Address Real-Life Challenges And Questions
Course Description
Discover the 7 Basic Quality Tools that drive continuous improvement and effective problem-solving in any organization.
These essential tools form the core of popular methodologies like Six Sigma (DMAIC) and Lean (Waste Reduction), making them a must-know for quality-focused professionals.
What You’ll Learn:
-
- How to leverage the Seven Basic Quality Tools—also known as “The Original Seven” or “Must-Know Quality Tools”—to achieve better process efficiency and quality outcomes.
- Insight into the origins and importance of these tools, as introduced by Kaoru Ishikawa, a pioneer in quality circles.
- A detailed understanding of each tool:
- Cause-and-Effect Diagram (Ishikawa/Fishbone)
- Check Sheet
- Control Chart
- Histogram
- Pareto Chart
- Scatter Diagram
- Flowchart
These tools can each deliver immediate value on their own, but their true power is unlocked when you apply them together, in the right order, and to the right challenges.
By mastering these tools, you’ll gain the skills to analyze processes, identify root causes, and implement sustainable improvements.
What’s Included:
-
- Step-by-step guidance on how to access and train with these tools, including complementary resources.
- A practical walkthrough example to help you apply these tools directly to your business, processes, or operations.
Join us for this 90-minute webinar and take a proactive step toward driving excellence and boosting productivity in your work environment.
Enroll Now!
Discover the 7 Basic Quality Tools that drive continuous improvement and effective problem-solving in any organization.
These essential tools form the core of popular methodologies like Six Sigma (DMAIC) and Lean (Waste Reduction), making them a must-know for quality-focused professionals.
What You’ll Learn:
-
- How to leverage the Seven Basic Quality Tools—also known as “The Original Seven” or “Must-Know Quality Tools”—to achieve better process efficiency and quality outcomes.
- Insight into the origins and importance of these tools, as introduced by Kaoru Ishikawa, a pioneer in quality circles.
- A detailed understanding of each tool:
- Cause-and-Effect Diagram (Ishikawa/Fishbone)
- Check Sheet
- Control Chart
- Histogram
- Pareto Chart
- Scatter Diagram
- Flowchart
These tools can each deliver immediate value on their own, but their true power is unlocked when you apply them together, in the right order, and to the right challenges.
By mastering these tools, you’ll gain the skills to analyze processes, identify root causes, and implement sustainable improvements.
What’s Included:
-
- Step-by-step guidance on how to access and train with these tools, including complementary resources.
- A practical walkthrough example to help you apply these tools directly to your business, processes, or operations.
Join us for this 90-minute webinar and take a proactive step toward driving excellence and boosting productivity in your work environment.
Enroll Now!
Why you should attend
In today’s competitive landscape, continuous improvement isn’t just an advantage—it’s a necessity.
Without it, businesses risk falling behind, losing their edge, and ultimately, their market share. Yet, many improvement methodologies are costly and complex, making it difficult for organizations to adopt them effectively.
This webinar offers a practical and affordable alternative, empowering you to drive improvement without the heavy investment.
Why This Training is a Must-Attend:
-
- Stay Ahead of the Competition: Learn how to apply proven quality tools that help you streamline processes, reduce waste, and improve efficiency, ensuring you maintain a competitive edge.
- Achieve Corporate Objectives with Confidence: By mastering the 7 Basic Quality Tools, you’ll gain the skills needed to identify root causes, resolve issues faster, and enhance overall quality—all without the high costs of complex systems.
- Simplify Problem-Solving: Get hands-on guidance on using each tool effectively to tackle everyday challenges, enabling smoother workflows and greater operational success.
- Affordable and Accessible: Unlike many improvement programs, this training focuses on practical, low-cost tools that can be implemented quickly and deliver immediate results.
- Career Advancement: Boost your professional credibility by adding essential quality management skills to your toolkit—skills that are highly valued across industries like manufacturing, healthcare, and service industries.
Don’t miss the opportunity to gain practical insights and hands-on experience that will help you and your organization thrive in a competitive market.
Join Now!
In today’s competitive landscape, continuous improvement isn’t just an advantage—it’s a necessity.
Without it, businesses risk falling behind, losing their edge, and ultimately, their market share. Yet, many improvement methodologies are costly and complex, making it difficult for organizations to adopt them effectively.
This webinar offers a practical and affordable alternative, empowering you to drive improvement without the heavy investment.
Why This Training is a Must-Attend:
-
- Stay Ahead of the Competition: Learn how to apply proven quality tools that help you streamline processes, reduce waste, and improve efficiency, ensuring you maintain a competitive edge.
- Achieve Corporate Objectives with Confidence: By mastering the 7 Basic Quality Tools, you’ll gain the skills needed to identify root causes, resolve issues faster, and enhance overall quality—all without the high costs of complex systems.
- Simplify Problem-Solving: Get hands-on guidance on using each tool effectively to tackle everyday challenges, enabling smoother workflows and greater operational success.
- Affordable and Accessible: Unlike many improvement programs, this training focuses on practical, low-cost tools that can be implemented quickly and deliver immediate results.
- Career Advancement: Boost your professional credibility by adding essential quality management skills to your toolkit—skills that are highly valued across industries like manufacturing, healthcare, and service industries.
Don’t miss the opportunity to gain practical insights and hands-on experience that will help you and your organization thrive in a competitive market.
Join Now!
Areas Covered
-
- Introductions: Set the stage with an overview of continuous improvement and its importance in achieving business excellence.
- Introduction to the Seven Basic Quality Tools: Gain an understanding of the core tools used in quality management, laying the foundation for process improvement.
- In-Depth Overview of Each Tool: Explore each of the Seven Basic Quality Tools individually, including:
- Cause-and-Effect Diagram (Fishbone/Ishikawa): Identify and analyze root causes of problems.
- Check Sheet: Efficiently gather and analyze data for informed decision-making.
- Control Chart: Monitor and control process variations over time.
- Histogram: Visualize data distribution for better insights into performance.
- Pareto Chart: Focus on the critical few to address major issues effectively.
- Scatter Diagram: Identify correlations between variables and improve predictive analysis.
- Flowchart: Map out process flows for streamlined operations.
- Standalone Value of Each Tool: Learn how each tool can be used independently to solve specific challenges in quality management and process improvement.
- Integrating the Tools for Continuous Improvement: Understand the synergy of using all seven tools together for a comprehensive problem-solving approach and how this integration drives sustained improvement.
- Practical Application Walkthrough: Follow a step-by-step example that demonstrates how to apply the tools to real-world scenarios, providing you with actionable insights to apply in your own organization.
BONUS:
-
- PDF copy of the presentation handout for your future reference.
- Soft copy of the certificate of completion on request.
- Q&A Session with the Presenter: Get your pressing questions answered verbally, via chat or email.
-
- Introductions: Set the stage with an overview of continuous improvement and its importance in achieving business excellence.
- Introduction to the Seven Basic Quality Tools: Gain an understanding of the core tools used in quality management, laying the foundation for process improvement.
- In-Depth Overview of Each Tool: Explore each of the Seven Basic Quality Tools individually, including:
- Cause-and-Effect Diagram (Fishbone/Ishikawa): Identify and analyze root causes of problems.
- Check Sheet: Efficiently gather and analyze data for informed decision-making.
- Control Chart: Monitor and control process variations over time.
- Histogram: Visualize data distribution for better insights into performance.
- Pareto Chart: Focus on the critical few to address major issues effectively.
- Scatter Diagram: Identify correlations between variables and improve predictive analysis.
- Flowchart: Map out process flows for streamlined operations.
- Standalone Value of Each Tool: Learn how each tool can be used independently to solve specific challenges in quality management and process improvement.
- Integrating the Tools for Continuous Improvement: Understand the synergy of using all seven tools together for a comprehensive problem-solving approach and how this integration drives sustained improvement.
- Practical Application Walkthrough: Follow a step-by-step example that demonstrates how to apply the tools to real-world scenarios, providing you with actionable insights to apply in your own organization.
BONUS:
-
- PDF copy of the presentation handout for your future reference.
- Soft copy of the certificate of completion on request.
- Q&A Session with the Presenter: Get your pressing questions answered verbally, via chat or email.
Who is this course for
Everybody Benefits from Watching This. Even Better When Done as a Group!
-
- Leaders Seeking to Empower Their Teams with Effective Problem-Solving Skills: Equip your team with the tools needed for continuous improvement and process optimization.
- Department Heads Aiming to Streamline Operations and Boost Efficiency: Learn practical quality tools that help identify inefficiencies and drive productivity.
- Professionals Looking to Advance Their Careers in Quality Management: Gain hands-on knowledge of essential tools used in Six Sigma and Lean methodologies.
- Training Managers Designing Comprehensive Learning Paths for Team Members: Integrate practical, low-cost tools into training programs for sustainable process improvements.
- HR Professionals Focused on Building a Culture of Continuous Improvement: Foster a quality-driven mindset across teams by introducing proven methodologies.
- Operations Managers Seeking to Reduce Waste and Optimize Processes: Learn how to apply quality tools that lead to cost savings and process improvements.
- Project Managers Handling Complex Initiatives with Tight Deadlines: Use these tools to diagnose issues quickly and ensure projects stay on track.
- Small Business Owners Who Want to Stay Competitive: Implement practical problem-solving techniques to maintain operational excellence without a large budget.
- Quality Assurance Professionals Aiming to Enhance Their Organization’s Standards: Master the core tools needed to improve quality control and reduce defects.
Everybody Benefits from Watching This. Even Better When Done as a Group!
-
- Leaders Seeking to Empower Their Teams with Effective Problem-Solving Skills: Equip your team with the tools needed for continuous improvement and process optimization.
- Department Heads Aiming to Streamline Operations and Boost Efficiency: Learn practical quality tools that help identify inefficiencies and drive productivity.
- Professionals Looking to Advance Their Careers in Quality Management: Gain hands-on knowledge of essential tools used in Six Sigma and Lean methodologies.
- Training Managers Designing Comprehensive Learning Paths for Team Members: Integrate practical, low-cost tools into training programs for sustainable process improvements.
- HR Professionals Focused on Building a Culture of Continuous Improvement: Foster a quality-driven mindset across teams by introducing proven methodologies.
- Operations Managers Seeking to Reduce Waste and Optimize Processes: Learn how to apply quality tools that lead to cost savings and process improvements.
- Project Managers Handling Complex Initiatives with Tight Deadlines: Use these tools to diagnose issues quickly and ensure projects stay on track.
- Small Business Owners Who Want to Stay Competitive: Implement practical problem-solving techniques to maintain operational excellence without a large budget.
- Quality Assurance Professionals Aiming to Enhance Their Organization’s Standards: Master the core tools needed to improve quality control and reduce defects.
Instructor Profile
José Mora is a Principal Consultant specializing in Manufacturing Engineering and Quality Systems. For over 30 years he has worked in the medical device and life sciences industry specializing in manufacturing, process development, tooling, and quality systems.
Prior to working full time as a consulting partner for Atzari Consulting, José served as Director of Manufacturing Engineering at Boston Scientific and as Quality Systems Manager at Stryker Orthopedics, where he introduced process performance, problem solving, and quality system methodologies. During that time he prepared a white paper on the application of lean manufacturing methods to the creation and management of controlled documents and a template for strategic deployment.
José led the launch of manufacturing at a start-up urology products company as Director of Manufacturing for UroSurge, Inc. at the University of Iowa’s business incubator park in Coralville, IA, creating a world-class medical device manufacturing operation, with JIT, Kanban systems, visual workplace and lean manufacturing practices.
José worked for 10 years at Cordis Corporation, now a Cardinal Health company, where he led the successful tooling, process development and qualification of Cordis’ first PTA (percutaneous transluminal angioplasty) catheter. His medical device experience includes surgical instruments, PTA & PTCA dilatation and guiding catheters, plastic surgery implants and tissue expanders, urology implants and devices for the treatment of incontinence, delivery systems for brachytherapy, orthopedic implants and instruments, and vascular surgery grafts and textiles.
During his time at Cordis, José managed the Maintenance and Facilities Department, taking that operation to a level rated as “tops” by the UK Department of Health and Social Services (DHSS) during one of their intensive audits. Jose managed Manufacturing Engineering as part of the Guiding Catheter Core Team of managers, a team that took the Cordis Guiding Catheter business to lead the market, bringing it up from fourth place. By introducing world-class techniques, the Guiding Catheter design and manufacturing was completely re-engineered for robust design and tooling, under Jose’s leadership.
He was also instrumental and played a leadership role in the complete re-engineering of the Tooling Control System, including design drafting, the tool shop and technical support. Wherever he has worked, he has a track record of introducing world-class methodologies such as Kepner-Tregoe, Taguchi techniques, Theory of Constraints, Lean Manufacturing, Five S (Visual Workplace), process validation to Global Harmonization Task Force standards, and similar approaches.